What is the last step of the cutter head?
Dora Zhang
2022-06-28 12:24:54
T shape stone cutting segment is sharp and durable with good performance. Marble and granite are often used as decorative materials.
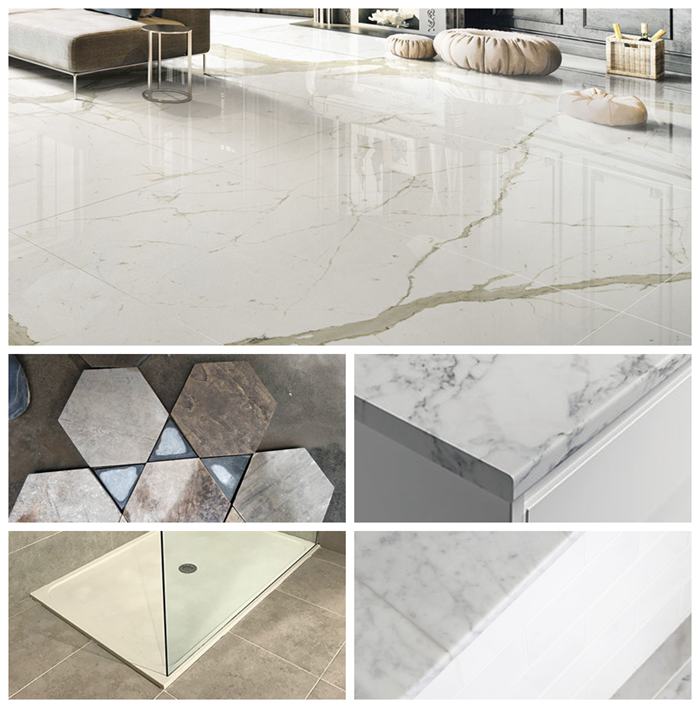
Sandwich Diamond Segment for cutting, cutting is a necessary process.
The cutter head is usually made by adding a certain amount of artificial diamond particles to specific metal powder and further sintering under high temperature and high pressure through powder metallurgy technology.
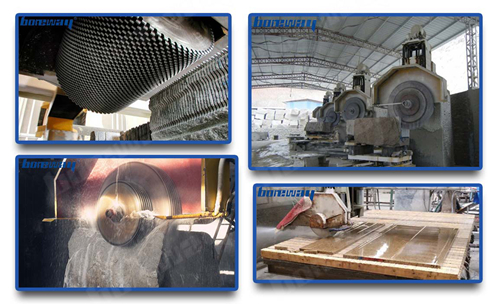
V shaped diamond segments for blade.We have Segments Type: Layer Type, "K" type, "V" Type, Grooved Type, M Type, Taper Type etc. Cutting granite from over 500 kinds of granite in many coutries. That have the main feature of fast cutting and long lifespan. Saving you more than 50% cost every year!
There are many steps to make a diamond bit, and the last step is cutting.
1) . cutting edge
The cutting edge is mainly to make the diamond fully exposed and convenient for direct use. In addition, it also plays a role in improving the accuracy and beauty of the tool. Generally, 50-70 strength range is used for cutting edge grinding wheel, with medium hardness (∅ 300mm-- ∅ 600mm). Generally, medium and large diameter saw blades are directly cut on the saw machine with fire-resistant and wear-resistant materials to achieve the best cutting effect;
(2) . leveling
The general leveling is for the old substrate (recycled substrate), and the method includes simple knocking and upper balancing instrument;
(3) Polishing
Put the tested saw blade (diameter 300-600) on the polishing machine and polish the substrate surface with 60 mesh or 80 mesh abrasive belt (once or twice) to achieve a beautiful effect and prepare for the next painting process;
(4) Painting
Clean the finished polished saw blade, and apply the spray paint water curtain system for spray paint processing as required;
(5) Marking and packaging
Product marking or laser marking shall be carried out as required, including product identification, saw blade rotation direction, safety identification, specification and model identification, etc.
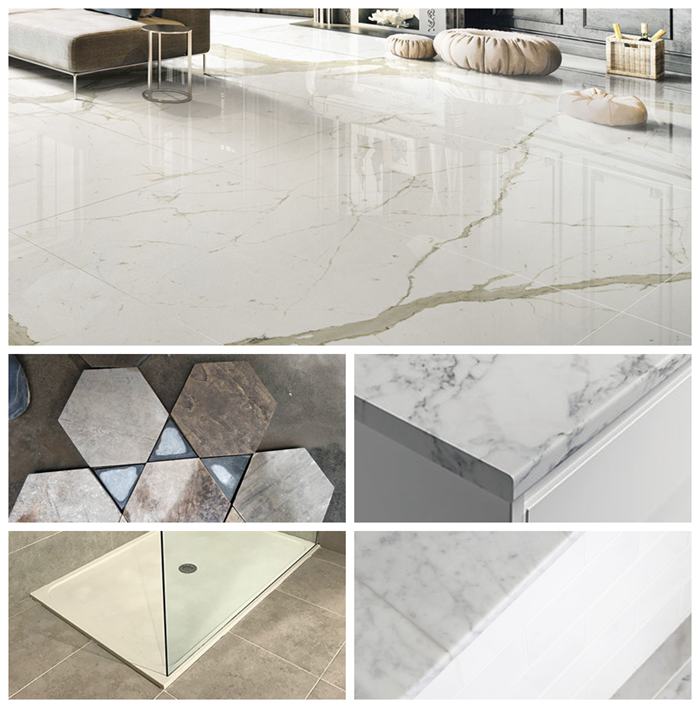
Sandwich Diamond Segment for cutting, cutting is a necessary process.
The cutter head is usually made by adding a certain amount of artificial diamond particles to specific metal powder and further sintering under high temperature and high pressure through powder metallurgy technology.
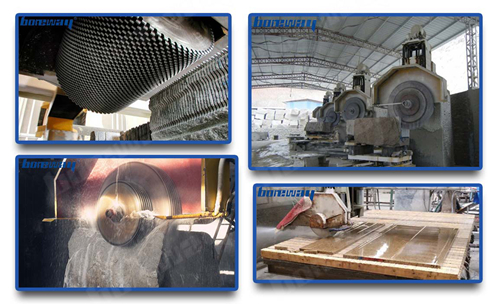
V shaped diamond segments for blade.We have Segments Type: Layer Type, "K" type, "V" Type, Grooved Type, M Type, Taper Type etc. Cutting granite from over 500 kinds of granite in many coutries. That have the main feature of fast cutting and long lifespan. Saving you more than 50% cost every year!
There are many steps to make a diamond bit, and the last step is cutting.
1) . cutting edge
The cutting edge is mainly to make the diamond fully exposed and convenient for direct use. In addition, it also plays a role in improving the accuracy and beauty of the tool. Generally, 50-70 strength range is used for cutting edge grinding wheel, with medium hardness (∅ 300mm-- ∅ 600mm). Generally, medium and large diameter saw blades are directly cut on the saw machine with fire-resistant and wear-resistant materials to achieve the best cutting effect;
(2) . leveling
The general leveling is for the old substrate (recycled substrate), and the method includes simple knocking and upper balancing instrument;
(3) Polishing
Put the tested saw blade (diameter 300-600) on the polishing machine and polish the substrate surface with 60 mesh or 80 mesh abrasive belt (once or twice) to achieve a beautiful effect and prepare for the next painting process;
(4) Painting
Clean the finished polished saw blade, and apply the spray paint water curtain system for spray paint processing as required;
(5) Marking and packaging
Product marking or laser marking shall be carried out as required, including product identification, saw blade rotation direction, safety identification, specification and model identification, etc.